Modeling of Nanofibers and Nonwoven Materials
Personnel: Sezen Buell
Electrospinning of polymeric nanofibers is a promising approach for development and commercialization of 1-D nanomaterials. Their combined characteristics of small fiber diameter (50-500 nm) and large surface area (10-100 m2/g) make polymeric nanofibers an exciting new class of materials that can be used in many applications such as filters, composites, fuel cells, nanowires, catalyst supports, drug delivery devices and tissue scaffolds. Of fundamental necessity for many of these applications is an understanding of the properties of individual nanofibers and their effects on the nonwoven material behavior.
In this area, our aim is to develop new models with which to investigate the size-dependent properties of polymeric nanofibers and to relate fabric properties to fiber properties by using multiscale modeling techniques. These structure-property models complement on-going efforts to model the electrospinning process. They are also essential to fill a gap between fabric measurements and fiber property characterization. The models themselves provide new insights into the relationships between fiber structure and electrospun fabric performance. In addition, the models serve as tools for future design of new materials and set goals for the production of fibers and fabrics with particular performance characteristics.
We are using molecular dynamics (MD) simulations to identify and evaluate the size dependent properties of polymeric nanofibers. The fibers consist of chains that mimic the prototypical polymer polyethylene (PE). We analyze these nanofibers for signatures of emergent behavior in their structural, thermal and mechanical properties as a function of the fiber radius. For sufficiently large diameter fibers, mass and energy density profiles attain bulk-like values at the center of the fiber. The chains at the surface of the fiber show conformational characteristics that differ significantly from those of chains at the center of the nanofiber. As the fiber size decreases, the glass transition temperature (Tg) and Young’s modulus (E) of the nanofibers decrease. A simple, 2-layer composite material model successfully captures the dependence of both Tg and E on the diameter of these nanofibers. According to this model, there is a surface layer which has a Tg that is depressed relative to Tg,bulk, characteristic of the center of the fiber. Similarly, the surface layer is more compliant than the center of the fiber. This softer, liquid-like surface layer affects both the thermal (Tg) and mechanical (E) properties.
For the continuum modeling of the nonwoven mat, we are using Monte Carlo methods. The nonwoven network is composed of several fibers that are represented by linked, cylindrical segments. Fiber flexibility is obtained by varying the material and geometrical properties of the segments in stretching, bending and twisting. We assume the elastic beam theory is valid for segments of fibers and our acceptance criterion is inversely related to flexibility of these segments. Using this model, we can create networks with randomly aligned fibers or fibers aligned in a certain direction by using this criterion. We have successfully simulated nonwoven networks with volume fractions of 5-25%, comparable to those of real electrospun nonwovens.
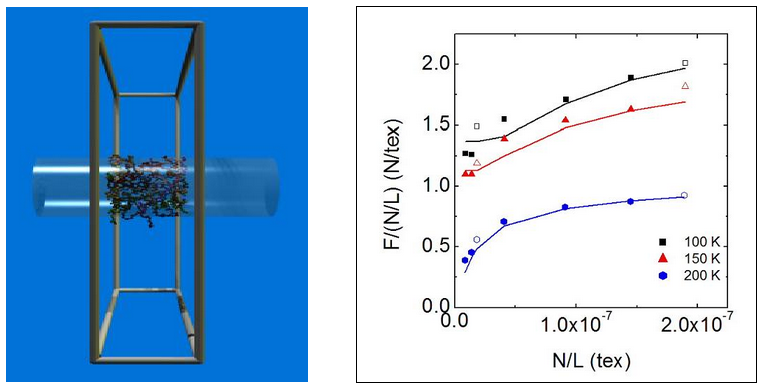